Understanding Tooling Molding: Elevating the Metal Fabrication Industry
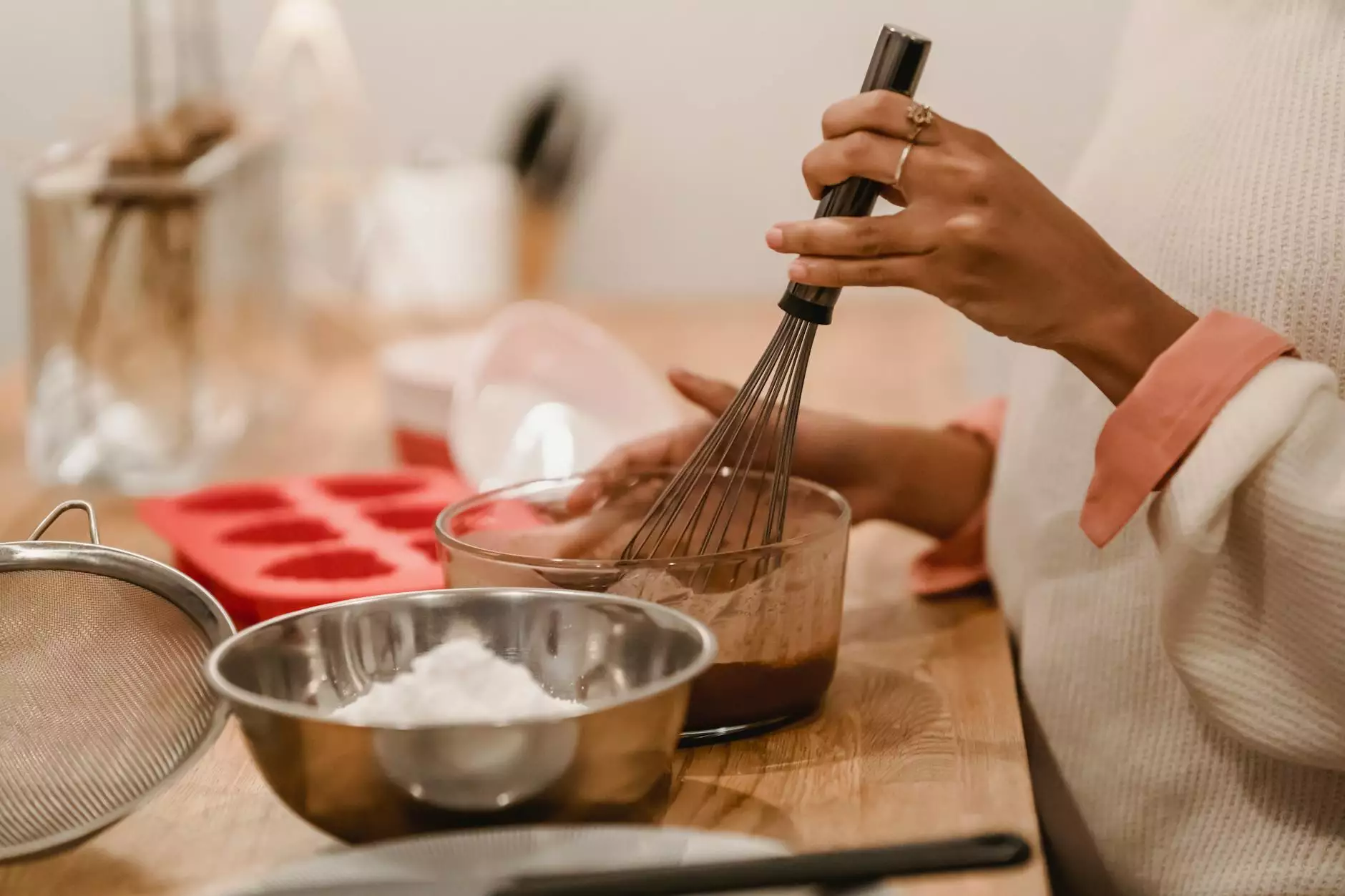
In the metal fabrication industry, the phrase tooling molding stands out as a transformative process that enhances efficiency, precision, and overall product quality. This technique plays a crucial role in the manufacturing processes across various sectors, ensuring that businesses can meet the ever-increasing demands of the market. This article delves deep into the nuances of tooling molding, its benefits, processes, and applications, specifically highlighting its significance for metal fabricators such as DeepMould.net.
The Basics of Tooling Molding
Tooling molding is a manufacturing process that involves creating tools (molds) that define the shape of a product. It is an essential technique utilized in the production of various metal components and parts, enabling manufacturers to replicate designs accurately and at scale. Here are the fundamental elements of tooling molding:
- Designing the Mold: The process begins with designing a mold that mirrors the desired final product. Advanced software tools, such as CAD (Computer-Aided Design), are often used to create precise 3D models.
- Material Selection: Selecting the right materials for the mold is vital. Common materials include steel and aluminum due to their durability and ability to withstand high temperatures.
- Production of the Mold: Once the design is finalized and the materials are selected, the mold is manufactured through processes like CNC machining or 3D printing.
- Testing the Mold: After production, the mold undergoes rigorous testing to ensure it meets quality standards and performs as expected.
The Process of Tooling Molding
The process of tooling molding can be broken down into several steps that contribute to the overall efficiency and effectiveness of metal fabrication:
1. Conceptualization and Design
Every great product starts with a concept. Initial discussions between engineers and designers establish the product's functionality and design requirements. During this stage, using software tools to create a 3D model is imperative, as it allows stakeholders to visualize the final outcome.
2. Prototype Development
Once the design is approved, a prototype of the mold is created. This prototype is crucial for detecting potential issues before the final mold is made. Rapid prototyping techniques such as 3D printing often come into play, allowing for fast adjustments and modifications.
3. Tool Construction
The construction of the actual tooling mold begins after prototyping. Manufacturers select high-grade materials suitable for high-volume production. This phase often involves machining processes that cut and shape the mold according to the specifications laid out during the design phase.
4. Mold Testing and Refining
Mold testing is essential. It involves producing sample parts using the mold to ensure that the components meet the required specifications. If discrepancies occur, adjustments are made to the mold design, followed by additional testing.
5. Production Using the Mold
With the mold tested and finalized, mass production can commence. The molds are loaded into machines that replicate the design, allowing for swift and uniform output. This phase highlights the efficiency gained through the use of tooling molding.
Benefits of Tooling Molding in Metal Fabrication
The impact of tooling molding within the context of metal fabricators is profound. Here are some key benefits:
1. Increased Efficiency and Productivity
By allowing for rapid replication of designs, tooling molding significantly enhances production speeds. Metal fabricators can efficiently produce large quantities of parts, thereby meeting customer demands without compromising quality.
2. Consistency and Quality Assurance
Tooling molding ensures that every product made through the mold is identical, which is crucial for maintaining brand reputation and product reliability. This consistency minimizes defects and reduces the need for extensive quality checks in later production stages.
3. Cost Efficiency
Investing in tooling molding may imply upfront costs, but the long-term savings are considerable. Mass production capabilities reduce labor costs per unit and streamlined operations lead to reduced waste and material costs.
4. Flexibility in Design Adjustments
Modern tooling molding methods incorporate advanced technologies, which allow for easy adjustments to designs without starting from scratch. This adaptability ensures that businesses can respond to market demands and customer preferences swiftly.
Applications of Tooling Molding in Various Sectors
The versatility of tooling molding means that it finds applications across numerous sectors, enhancing its relevance in today’s economy. Here are some primary industries benefiting from this technique:
1. Automotive Industry
The automotive industry heavily relies on tooling molding for producing metal parts such as engine components, chassis elements, and exterior features. Fast production and high-quality standards are paramount in this sector, making tooling molding indispensable.
2. Aerospace Sector
In aerospace, the precision required for parts is critical for safety and performance. Tooling molding allows manufacturers to create lightweight, durable components that meet stringent compliance standards.
3. Electronics Manufacturing
With the increasing demand for electronic devices, tooling molding aids in producing housings and intricate soldering components, ensuring that production meets the high-tech industry's quick turnaround requirements.
4. Medical Equipment
The medical field necessitates an unparalleled level of precision. Tooling molding helps produce surgical instruments and equipment components that require strict adherence to tolerances, ensuring patient safety and equipment reliability.